Founded in 2005, Sunchine Inspection is one branch of Sunchine International; a Hong Kong based multinational company specializing in export-import consulting and quality management. Today, with two offices in China mainland and one office in Europe, Sunchine Inspection has become one of the best third party inspection companies in China, serving over 1,500 regular clients in various fields from all the Continents in the world.
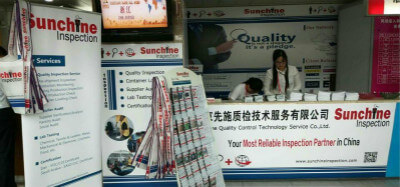
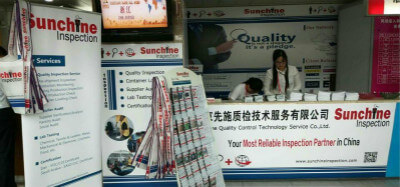
BY RENAUD ANJORAN
Now I am assuming that you have decided to source in China by yourself.
One key point I want to communicate is this: you need to follow a process. You CANNOT browse a website, send a few emails, respond, and see where it takes you.
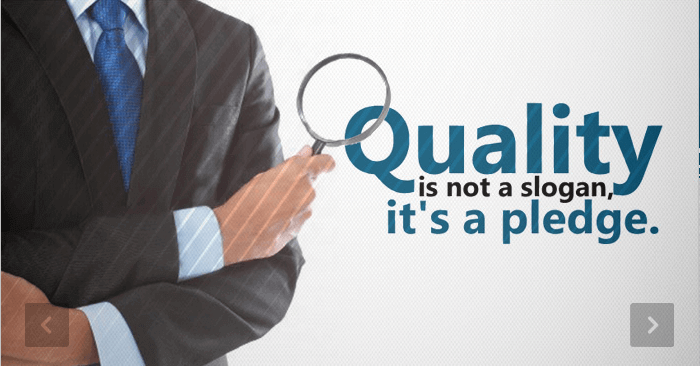
If you want a written checklist that you can adapt and follow, you will find an example here. It deals with sourcing, development, production, and transportation (but it is not applicable if you develop your own product).
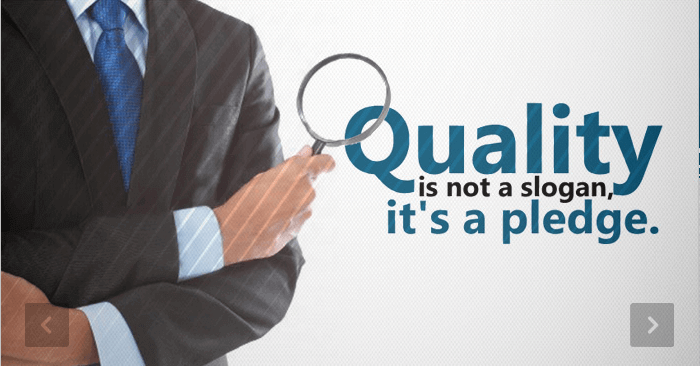
If you want a written checklist that you can adapt and follow, you will find an example here. It deals with sourcing, development, production, and transportation (but it is not applicable if you develop your own product).
But let’s look at the sourcing process first in more detail. It includes 2 steps:
- Identifying potential suppliers;
- Screening these suppliers and verifying the last candidate(s).
For now, let’s focus on the first step, which itself includes 3 sub-steps:
Sub-step 1. Drawing your ideal supplier profile
Ask yourself a few questions:
- Do you need a supplier with strong engineering capabilities (to develop new products)?
- Do you need them to have a wide range of designs that you can choose from?
- Do you want them to focus on low cost? Or on high quality?
- How big should they be? This is a very important criterion for the reasons discussed below. You will encounter factories belonging to these 3 levels, and their performances and prices will be vastly different:
Here is my general advice on the topic of the supplier’s size:
- If your orders are very small, you might need to work with a trading company that will place your orders in a level 1 factory and (hopefully) follow production closely.
- If your orders are large enough to work directly with a manufacturer, but not big enough to be interesting to big factories, go for level 2 (250-800 workers, roughly).
- If your orders are considered large and you find the big companies actively fighting for your business, then level 3 is good for you.
Sub-step 2. Go to online B2B directories and/or trade shows
If you can get the opportunity to go to a trade show (Canton Fair, China Sourcing Fairs, and so on) that deals with your product category, go there! Ask a few open questions, the objective here is to eliminate any supplier that doesn’t fit with your ideal profile.
If you can’t physically get to a trade show, you will need to use B2B directories. Beware! They function like the yellow pages (suppliers who pay more, get their products featured more prominently). There is not as much effort to avoid listing bad apples as you might think.
Make sure you look at the information inside the profiles, to target only those suppliers that correspond to your ideal profile. For example, by keeping only suppliers with a minimum capital of 1 million RMB or above (this information is available on several supplier directories, I believe), you are eliminating 99% of trading companies from your search results.
Sub-step 3. Motivate potential suppliers to respond to you
Most suppliers get too many inquiries and need to choose which ones they respond to. Here are a few tips to get their attention.
- The first message should be short, less than 8 lines if possible (including the product description), and with a VERY CLEAR call to action (“get back to me if you want more information about our needs”).
- If you have a product specification sheet, share it with them and get their feedback. You should expect them to ask questions about manufacturing, like material specification or, if they don’t accept your tolerances, etc., if they say, “it’s fine”, this is not always a good sign.
- And then… Follow up fast in responding to their questions, and finalize your screening process within 8 days. After that, your inquiry, in their eyes, will have gone cold.
- If possible, call them (most of them have a Skype account and they all have a Wechat account — these 2 applications allow you to make calls for free if both parties are connected). Show that you are human and that you are investing your time to get to know them.
A big mistake to watch out for
http://www.tripntale.com/profile/113192/fuh7swaaa9ehttp://www.tripntale.com/profile/113194/nedwymmoouoodhttp://www.tripntale.com/profile/113195/dx9zzqnsgn3ihttp://www.tripntale.com/profile/113193/n6ce6fhjddhttp://www.tripntale.com/profile/113196/ejdvyzp5dhttp://www.tripntale.com/profile/113198/dokulangt3qphttp://www.tripntale.com/profile/113197/lvdswahzdshttp://www.tripntale.com/profile/113199/ddiwffvg0vhttp://www.tripntale.com/profile/113201/dbuebkzyucuvhttp://www.tripntale.com/profile/113200/akoubf0esddhttp://www.tripntale.com/profile/113202/aavywojj9f8hdhttp://www.tripntale.com/profile/113168/mcreynolds12http://www.tripntale.com/profile/113170/e6286dhttp://www.tripntale.com/profile/113169/x5173973http://www.tripntale.com/profile/113171/r7317395http://www.tripntale.com/profile/113172/f9517395http://www.tripntale.com/profile/113174/x517dd3973http://www.tripntale.com/profile/113176/ss3lby8c
Some potential suppliers will offer a price that is much lower than average. How is this possible?
- Some suppliers want to start developing a product with you, and they will use tactics to increase the price along the way (usually after the deposit for the first order has been wired).
- Some other suppliers simply don’t know what the costs are. They have never made this product, even though you found it in their showroom. They will wonder where and how to manufacture it after you have sent them a PO. This is also a bad sign.
So, how to do?
You will likely see several very similar quotes from different suppliers: that’s the “market price”. Eliminate all the “outliers” that gave prices 20% higher or lower than the average. (If you are consciously looking to buy above the market price to get above-average quality, keep the highest quotes).
End of the identification phase
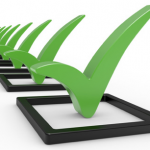
The next step is to screen most potential suppliers out, and to verify the last one or two in more depth. That will be covered in the next post in this series. https://www.sunchineinspection.com/